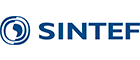
SINTEF is the largest independent contract research organization in Scandinavia and the 4th largest in Europe with approximately 2000 employees (70% of them are researchers, 53% of them have PhD degree).
SINTEF is a broadly based, multidisciplinary research institute with international top-level expertise in technology, medicine and the social sciences. SINTEF conducts contract R&D as partner for the private and public sectors, creating value and developing solutions to some of society’s grand challenges by being at the forefront of the following strategic focus areas: renewable energy, climate- and environmental technology, oil and gas, ocean space technology, health and welfare and enabling technologies.
One of SINTEF’s business areas participating in the present proposal is SINTEF Materials and Chemistry, which offers high competence within materials technology, applied chemistry and applied biology. The research division performs research and development, advanced consultancy and laboratory services. SINTEF Materials and Chemistry works closely with industry in development of advanced materials, products, processes and new tools, and seeks out new, environmentally friendly processing methods that will increase productivity and raise quality standards.
SINTEF is a leading participant in EU’s research programs, with a total of 240 projects. The division SINTEF Materials and Chemistry is up to date participating in 39 projects, 26 in 7FP and 13 in H2020, 14 of them as coordinator.
Role in the project and main tasks
SINTEF was the Coordinator and technical leader, and was also involved in dissemination and exploitation activities. Moreover SINTEF performed (and led) the tasks dealing with extraction of Rare Earth Alloys (REA) by high temperature electrolysis methods.
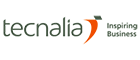
TECNALIA (http://www.tecnalia.com/en/) is the leading private and independent research and technology organization in Spain and one of the largest in Europe, employing 1,400 people. The current proposal will be carried out by the Energy and Environmental Division, where more than 250 people are focusing their R&D effort to the development of technologies, products and tools for a rational and sustainable use of energy focusing on clean generation sources and future energy carriers. In particular, the Material for Energy and Environment Area of this
division will involve their researchers and facilities in this proposal. TECNALIA’s expertise are in the development of IL based processes for different applications such as
metal extraction from different industrial waste streams, surface treatment, coatings, and electrolytes for batteries. It has extensive capabilities for design, synthesis and characterization of IL with tailored properties for specific applications (e.g. metal extraction, etc). In addition, the area is growing in more IL-related research fields such us recycling and other energy and environment related applications.
Role in the project and main tasks
TECNALIA’s role in REE4EU includeed the extraction and separation of “REE” by Ionic Liquid Extraction. TECNALIA was involved in selective precipitation of REE for added value REO mixtures which was sent to SINTEF. TECNALIA developed these activities at lab scale and supported pilot activities. Moreover, replication of IL into NiMH batteries wastes and support for pilot activities were carried out.
LCM is a world leader in the manufacture and supply of Rare Earth element (REE) based alloys and high purity metals. With considerable experience in the production of materials to tight compositional tolerances and controlled microstructures, LCM offers an innovative and highly flexible approach to a wide range of material requirements. In 2008 LCM became part of the Canadian mining company, Great Western Minerals Group which is implementing a “Mine to Market” model to develop a fully integrated supplier of Rare Earth Alloys (REA). The group is fully committed to redevelopment of the Steenskampskraal monazite mine in South Africa which will provide a politically independent source of separated Rare Earth Oxide (REO) mixtures. These will become an input for the metal extraction and alloy plants already in process of being established and expanded to meet the increasing demands of European and Japanese magnet producers.
Role in the project and main tasks
LCM is one of key producers of speciality materials and metals in Europe, collaborating with various RE value chains, from permanent magnets to batteries production. LCM is moreover part of a mining company, as such extending the value chain upstream and opening-up future opportunities to evaluate REE4EU technology solutions to valorise mining waste (tailings). LCM was key to the REE4EU project as they installed the novel RE recovery processes, based on the novel HTE REA production process in combination with ILE or HM pre-treatment. LCM demonstrated that the new HTE process could actually be integrated in their existing RE Alloy production process with HM pre-treatment.
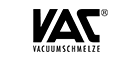
VAC is one of the world leading producers of high end metallic magnetic materials including sintered Rare Earth permanent magnets as well as melt spun amorphous or nanocrystalline soft magnetic alloys. VAC is the largest producer of sintered Nd-Fe-B and Sm-Co magnets in Europe. Consequently VAC has detailed competences regarding the powder metallurgical production of Rare Earth transition metal alloys and parts on an industrial scale. In addition VAC has large experience in the design and production of magnet assemblies for the automotive industry, MRI systems and scientific applications like wigglers and undulators.
Role in the project and main tasks
VAC made its in-process waste as well as EoL PM waste available as feedstock for the new REA recovery processes and used its pilot PM manufacturing facilities available to validate the outcome of the various novel HTE based RE recovery routes, in real PM manufacturing and test product quality.
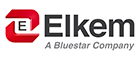
ELKEM is one of the world´s leading companies for environment-friendly production of metals and materials. The main products are silicon, solar grade silicon, special alloys for the foundry industry, microsilica and carbon.
ELKEM’s centre for corporate R&D, ELKEM AS Technology, is located in Kristiansand in Norway with approximately 100 employees. The R&D Technical Centre has facilities for doing lab scale and larger scale melting trials and testings of raw materials together with a well-equipped laboratory for chemical analyses and material characterization.
ELKEM has a 110 year of experience and competence within high-temperature metallurgical processes. There is a large portfolio of pyro metallurgical and hydro metallurgical equipment and experience in up-grading of biproducts, testing of raw materials, testing of equipment, process development and verification and product development and testing.
The R&D Technical Centre also includes a design group, mechanical, electrical, instrumentation and graphite workshops, as well as fully-equipped laboratories for chemical analysis and material characterization.
Role in the project and main tasks
ELKEM was key to the REE4EU project as they installed (together with LCM) the novel RE recovery processes, based on the novel HTE REA production process in combination with ILE or HM pre-treatment. ELKEM set-up in their facilities a fully new combined HTE and ILE pre-treatment, as such offering a pre-industrial scale benchmarking environment for the direct RE recovery routes from different waste streams 1) direct HTE REA production from PM and BAT EoL waste, 2) THE REA production with ILE pre-treatment of in-process and EOL PM waste, 3) HTE REA production with HM pretreatment on EoL PM and BAT waste.
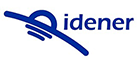
IDENER is a private research SME company composed of a team of researchers with a sound scientific background in disciplines comprising the branch of systems engineering, such as electronics and computer, systems integration and control, and process engineering. The company, located in Aerópolis Science and Technology Park (Seville, Spain), was founded in 2010 by a group of PhD holding engineers. From that time forward, IDENER has positioned as a valued partner of top European Research centers, Universities and technology firms.
IDENER investigated in the multidisciplinary field of Computational Science and its application to the optimization of systems and processes in key areas: Industrial Technologies; ICTs; Biotechnology; Secure, Clean and Efficient Energy; and Resource and Raw Materials Efficiency. This approach results in a high added value which sharpened the competitive edge of complex systems by providing improvements in performance and cost effectiveness. To that end, we at IDENER integrated concepts from four interrelated and complementary areas of knowledge: Mathematical Modeling and Simulation; Multidisciplinary Design Optimization; Control Engineering; and Software Engineering. This way, we aimed to contribute to the progress of AI setups and to update systems and processes in key areas in response to these incremental developments.
IDENER applied the knowledge from previous areas to several research specialties, one of them being “Resource and Raw materials efficiency”. Specifically, main activities in this area were
- Extraction and recovery of raw materials, especially from secondary sources. Example of this application are the recovery of Germanium from fly ash or REE from wastes
- Study and development of new approaches for extraction based in the use of ionic liquids.
- Tools for effective decision making and public engagement through the integration of knowledge and decision support frameworks (algorithms)
- Process monitoring and modelling, e.g. modelling of the Copper leaching process and its optimisation at industrial scale
- Multidisciplinary Design Optimisation (MDO) of mineral processing. Use of such information for conceptual and basic engineering
- Knowledge improvement on the availability of raw materials
- Fostering of resource efficiency through digital systems
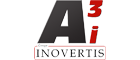
A3I is a French engineering firm (SME – 35 people), subsidiary of Inovertis (www.inovertis.fr), a group whose mission is to bring all areas of industrial process together. Its services range from technical studies, expert mission (ventilation, fluid networks, risk analysis, heat exchange calculations, regulatory files, etc.), processes design and engineering (drawing, 3D modelling, technical and economic feasibility, onsite implementations) and consultancy. Its departments of expertise include: 1) Chemical manufacturing; 2) Process engineering; 3) Mechanical engineering; 4) Fluid systems and ventilation; 5) Clean technologies The clean-tech department has an extensive experience in LCA and ecodesign of technologies.
Role in the project and main tasks
A3i-INOVERTIS was (1) be in charge of the detailed engineering of the ILE in view to build it in the ELKEM facility (2) led the Life Cycle Assessment of the Rare-earth element recovery processes developed in the project: ILE, HTE as well as the HydroMetallurgical routes. Data collection for the LCA was conducted in close collaboration with partners. Two types of REE-sources were considered: wastes of permanent magnet and batteries. The evaluation of the technologies moreover included social elements such as employment, job quality, human health, etc
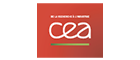
CEA is the French Alternative Energies and Atomic Energy Commission (Commissariat à l’Energie Atomique et aux Energies alternatives). It is a public body established in October 1945 by General de Gaulle. A leader in research, development and innovation, the CEA mission statement has two main objectives: to become the leading technological research organization in Europe and to ensure that the nuclear deterrent remains effective in the future. The CEA is active in four main areas: low-carbon energies, defense and security, information technologies and health technologies. In each of these fields, the CEA maintains a cross-disciplinary culture of engineers and researchers, building on the synergies between fundamental and technological research, e.g. by using large instruments for fine characterization of materials and systems. The total CEA workforce consisted of 15 800 employees. The concept of resource efficiency is an important task addressed by CEA for both material and energy (used in buildings, transportation and industry). The CEA has the determination to strengthen its partnership with other research agencies, universities and education and training institutions, which will enable CEA to spread its research within international coordinated projects.
Based on the knowledge developed in metal separation by HydroMetallurgy, CEA is getting involved in projects on the extraction/separation and valorisation of critical metals. For 6 years CEA teams located in Grenoble started to work on the recycling of the devices developed internally, such as batteries (Li-ion, NiMH,…), fuel cells, solar panels and more recently permanent magnets by setting up recovery techniques for valuable metals or materials.
Beside these activities, an historical expertise on powder metallurgy processes has led to development for magnetic materials synthesis, shape forming and complete testing. Among them a large focus is put on permanent magnet development with lower REE content.
Role in the project and main tasks
CEA mainly worked on replication for NiMH batteries. The work carried out on HM at lab scale was upscaled in an industrial leaching cell (5Liters). The CEA provided raw materials and dealt for upscaling partners with IDENER (modeling) and SINTEF (HTE process). The HM process developed for PM was declined and tuning for spent NiMH batteries. The data were used for the subsequent pilot design and HM pilot test on various sources of spent NiMH batteries. The work on the scaling up was done to accompany SNAM for piloting their HydroMetallurgical process. This includeed effort on the improvement and reliability of the HydroMetallurgical processes.
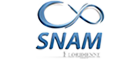
SNAM is a French company. It belongs to the Belgium Group «Floridienne» and employs around 100 people in two sites in France (Viviez and Saint Quentin Fallavier). Its core activity is the recycling of rechargeable batteries (Nickel cadmium, Nickel Metal Hydride, and lithium ion).
SNAM is an European leader for the following activities: recovery of cadmium, recycling of NiCd, NiMh and Li-ion battery). It also recycles alkaline and zinc carbon batteries and has developed sorting and battery recognition facilities. Its supplies come from a network of European and international collectors of spent portable and industrial batteries. SNAM annual recycling production in 2013 was around 3.000 ton of NiCd, 300 ton of NiMH and 200 ton of Li-Ion. SNAM is acting in all European countries (95% of its turnover), but is also active in Northern and Southern America, Asia or the Middle East. Its activity concentrates mainly on the recycling of portable batteries coming from gross collection schemes, as well as industrial batteries coming from industrial partners. In that aspect, SNAM has a historical collaboration with the French and German manufacturers of NiCd batteries SAFT and Hoppecke.
On the other side, SNAM developed recently contractual agreements with international groups from the automotive industry such as Honda, Toyota, PSA Volkswagen or BMW. These agreements concern the collection in Europe and the recycling of their End-of-Life EV and HEV batteries, as well as their production waste.
Role in the project and main tasks
SNAM had a wide experience in recovering metal with different processes. With an active collaboration in different projects, SNAM has developed knowledge and also a network for collecting the batteries and selling the material. SNAM participated in the replication for NiMh Batteries. SNAM has legal authorization in order to deal with waste and with such a process.
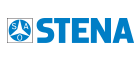
STENA, STENA Metall AB, is a family owned recycling company operating mainly in the northern parts of EU with the majority of the businesses in Sweden, Denmark, Norway, Finland, Poland, Germany and Italy. Annual turnover about 3 billion € and 3500 employed. Main daughter companies relevant for this project are STENA Technoworld AB, one of the larger (Waste Electrical and Electronic Equipment) WEEE-recyclers in EU, STENA Aluminium AB, the only secondary Al smelter in Sweden and STENA Recycling International. STENA Technoworld recycle electronic waste containing REE, like hard disc drives (HDD) but is today focusing on Cu and permanent magnets(PGMs). STENA Aluminium has melting capacity and air pollution control equipment suitable to handle gases from high temperature electrolysis. STENA Recycling International collects magnets from eg swarfped Wind Turbines parks.
Role in the project and main tasks
STENA brought into the consortium the expertise and interest of the Waste Recycler into the in-process oriented REE4EU project. STENA was responsible of dismantling of different types of magnets from WEEE like hard disk drives. Magnets needed to be characterized and monitored in relation to content of REE, binder, corrosion protection, contaminants. STENA also played a key role in PM and NiMH Batteries Value Chain and Market Analysis.
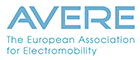
AVERE, founded in 1978, is a European network including Users, NGO’s, Associations, Interest groups, Public Bodies, Research and Development entities, Vehicle and Equipment Manufacturers, Electricity Utilities. Its main objective is promoting the use of Battery, Hybrid and Fuel Cell Electric Vehicles in order to achieve greener mobility for cities and countries. The main activities to achieve these objectives are related to dissemination, networking, monitoring, participation in European and multilateral projects, lobbying, research and development, among other. In public policy advocacy AVERE presents the electric drive industry’s and R&D bodies’ concerns to the European Commission.
Role in the project and main tasks
The REE4EU project built on recent highly promising research results to develop and validate a completely new 2-step REE recovery technology and process for both in-process and End-of-Life waste, which is highly flexible, potentially applicable to various REEs and cost effective, as such opening the route towards large volume REE recovery for various European value chains, including NiMH batteries. AVERE joined the consortium to support dissemination activities through Europe and beyond within the relevant REE demanding electric vehicles sector.
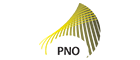
PNO Innovation, part of the PNO Innovation B.V., is specialised in Innovation Management and funding, providing support services to private and public organizations in Innovation processes, Technology Transfer, IT solutions and funding for research, development and innovation. PNO is a European group, made up of a pool of around 250 professionals including scientists, engineers, consultants, a Brussels policy advisory service, as well as financial and legal experts, with consolidated experience in innovation processes and funding in international working environments (Europe, Latin America, and USA). Created in 1985, PNO is a high-growth knowledge intensive company, operating in 12 European countries. The growth is explained by a unique combination of services, based on profound insight in research, innovation and funding strategies, up-to-date knowledge and over 25 years of hands-on expertise with real-life European innovation projects and more than 500 funding programmes in most EU countries. The company has the proven capability to link innovation suppliers and adopters from a unique Europe – wide client network in multiple sectors, using advanced methodologies, ICT solutions and proprietary on-line networking. PNO has its own community building, management and dissemination tools, the core one being Innovation Place © www.innovationplace.eu. With Innovation Place, PNO offers its clients an innovative service concept, up-to-date web-based tool, knowledge base and European wide communities to manage their own innovation, projects, funding knowledge and networks, combined with the best consultancy support.
As key advisor to the European Technology Platform (ETP) SusChem, the European Council for the Chemical Industry (CEFIC) and Association SPIRE PNO supports the development of medium to long term research and innovation agendas for resource efficiency.
Furthermore, PNO recently co-managed the process of developing a Public Private Partnership and the SPIRE 2030 Innovation Roadmap (www.spire2030.eu) for the sustainable process industry, as input to HORIZON 2020.
Role in the project and main tasks
PNO brought its international consulting experience into the consortium including extensive project and innovation management, exploitation and business planning expertise. A particular focus was given to market analysis, value chain stakeholders analysis, business planning, communication, exploitation and dissemination (CED) strategies and part of their execution. PNO also had a role in the consortium management activities.

CEFIC, as the voice of the European chemical industry, is a committed partner to EU policymakers, facilitating dialogue with industry and sharing its broad-based expertise. CEFIC represent 29,000 large, medium and small chemical companies in Europe, which directly provide 1.2 million jobs and account for 17% of world chemical production. Based in Brussels since its founding in 1972, CEFIC interacts every day on behalf of its members with international and EU institutions, non-governmental organisations, the international media, and other stakeholders. CEFIC has been one of the main drivers and is key facilitator of the SPIRE roadmap and association, collaborating with 7 other process industries to deliver impact in innovation for energy and resource efficiency towards a more competitive European process industry sector.
Role in the project and main tasks
The REE4EU project built on recent highly promising research results to develop and validate a completely new 2-step REE recovery technology and process for both in-process and End-of-Life waste, which is highly flexible, potentially applicable to various REE and cost effective, as such opening the route towards large volume REE recovery for various European value chains. CEFIC supported dissemination activities through Europe and beyond within the relevant Process and Chemical industries with particular attention to the EIP RM and SPIRE frameworks.
The UPS’ Laboratoire de Génie Chimique (LGC – UMR5503), Toulouse, France is managed by CNRS together with Université Toulouse III Paul Sabatier (UPS) and the Institut National Polytechnique de Toulouse (INPT). The team Molten Salts and Electrochemical Processes is expert in the field of physico-chemical properties, kinetics, thermodynamics, chemical engineering and electrochemistry.
The group studies new electrochemical processes in molten salts (separation, oxide conversion into metal, recycling…) or to optimize existing processes.
Role in the project and main tasks
UPS complemented SINTEF expertise in the field of HTE as well as facilitated the interaction with the some of the consortium partners, including CEA and SNAM. In particular UPS focused on HTE solutions for Spent Permanent Magnets and for other End-of-Life wastes, such as Spent Batteries, both at laboratory (especially) and pilot scale.